Woven patches Sono un elemento fondamentale nel branding dell'abbigliamento. Dalle etichette di moda agli abiti da lavoro e alle uniformi, offrono un modo elegante, durevole e dettagliato per incorporare loghi, nomi e messaggi nei prodotti in tessuto. Tuttavia, una sfida tecnica che viene spesso trascurata è solidità del colore—la capacità del cerotto di mantenere il suo colore originale dopo il lavaggio, l'esposizione alla luce o l'uso prolungato.
Se lavori nel settore dell'abbigliamento o ordini custom clothing labels Per il tuo brand, sai che una macchia sbiadita può compromettere la qualità del prodotto e incidere sulla soddisfazione del cliente. In questo blog, analizzeremo le cause dei problemi di colore nelle macchie di tessuto e come evitarli implementando pratiche di progettazione e produzione intelligenti.
Cosa sono le toppe tessute?
Woven patches Vengono create utilizzando fili intrecciati su un telaio per formare disegni intricati, proprio come la tessitura di tessuti. Rispetto alle toppe ricamate, che si basano su un filo cucito su una base, le toppe tessute possono ottenere grafiche più dettagliate e finiture più uniformi, rendendole ideali per loghi con testo di piccole dimensioni o dettagli raffinati.
Vengono spesso utilizzati per:
- Etichette con marchio sui capi di abbigliamento
- Decorazioni per cappelli e borse
- insegne uniformi
- Promotional merchandise
Nonostante i loro numerosi vantaggi, le toppe tessute possono presentare discrepanze di colore se non vengono prodotte sotto rigorosi controlli di qualità.
Problema reale: sbiadimento del colore dopo il lavaggio
Un caso recente che ha coinvolto un marchio di abbigliamento di alta gamma illustra bene il problema. L'azienda ha ordinato grandi quantità di etichette tessute personalizzate, solo per scoprire durante i test di lavaggio pre-spedizione che alcune etichette presentavano una leggera decolorazione. Sebbene lo sbiadimento non fosse particolarmente evidente, il cliente, noto per i suoi rigorosi standard qualitativi, ha sollevato preoccupazioni circa il potenziale degrado del colore a lungo termine una volta che i capi fossero stati consegnati al consumatore.
Dopo un'indagine, è stata identificata la causa principale: il filo utilizzato per lo sfondo grigio scuro era stato conservato in un ambiente umido per un periodo prolungato. Ciò ha portato a assorbimento incoerente del colorante, in particolare nelle aree con una saturazione del colore più intensa. Sebbene il metodo di produzione fosse tecnicamente valido, le condizioni ambientali e l'invecchiamento del materiale causavano un problema prevenibile.
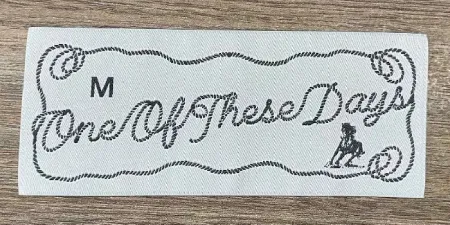
Come garantire la resistenza dei colori delle etichette tessute
Per affrontare il problema dello sbiadimento e prevenirne il ripetersi in futuro, il produttore ha implementato una strategia correttiva in tre fasi. Questi passaggi sono applicabili a qualsiasi azienda che desideri migliorare la qualità e la longevità dei propri prodotti. etichette tessute resistenti al colore.
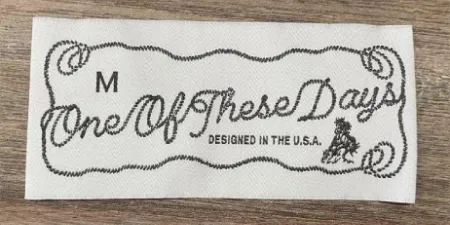
1. Utilizzare filo ad alta resistenza del colore
Il primo passo è stato sostituire il filo esistente con un filato certificato di alta qualità, classificato al Livello 4 o superiore nei test internazionali di solidità del colore. Questi fili sono specificamente progettati per resistere a molteplici cicli di lavaggio, sfregamenti ed esposizione ai raggi UV senza sbiadire in modo significativo.
Suggerimento: chiedi sempre al tuo fornitore di toppe informazioni sulla resistenza del colore dei suoi fili: questa semplice domanda può aiutarti a evitare seri problemi di qualità in futuro.
2. Aggiungi trattamenti di post-elaborazione
Una volta realizzate le toppe tessute, queste venivano sottoposte a impostazione ad alta temperatura processo seguito da un trattamento fissativo del coloreQuesti passaggi aggiuntivi rafforzano il legame delle molecole di tintura con il filo, rendendo i colori più resistenti al dilavamento o allo scolorimento durante il lavaggio.
Suggerimento: per le toppe utilizzate su abbigliamento sportivo, abbigliamento per bambini o uniformi, la post-elaborazione non dovrebbe essere negoziabile.
3. Eseguire rigorosi test di lavaggio
Prima di approvare il lotto finale, il team ha eseguito tre cicli di intensi test di lavaggio e attrito, ciascuno della durata di 45 minuti in acqua calda. I risultati sono stati verificati da un laboratorio esterno e condivisi con il cliente per confermare la conformità alle sue aspettative di qualità.
Suggerimento: non saltare mai il campionamento e i test di pre-produzione. Le simulazioni reali spesso rivelano problemi che non sono evidenti durante le ispezioni visive.
Perché è importante
When it comes to custom clothing labels o patch, l'estetica da sola non basta. I tuoi prodotti devono resistere all'uso quotidiano: lavaggi, sudorazione, stiramenti ed esposizione al sole. La resistenza del colore è un fattore cruciale, ma spesso sottovalutato, per garantire una qualità costante.
I marchi che adottano scorciatoie in termini di qualità dei coloranti o controlli ambientali potrebbero ritrovarsi a dover affrontare resi di prodotti, reclami dei clienti e danni alla reputazione. Investire in materiali di alta qualità e test rigorosi in anticipo può far risparmiare costi significativi e stress in futuro.
Considerazioni finali: il colore che dura crea marchi che durano
Ogni toppa tessuta che produci riflette l'attenzione ai dettagli e l'impegno del tuo brand per la qualità. Dando priorità alla resistenza del colore e collaborando con fornitori esperti e attenti alla qualità, puoi essere certo che i tuoi prodotti non solo saranno belli fin da subito, ma continueranno a stupire anche dopo mesi di utilizzo.
Che tu sia una startup di moda che ordina la tua prima tiratura di toppe tessute o un produttore di abbigliamento esperto che cerca prestazioni migliori dalle proprie etichette, concentrandosi su etichette tessute resistenti al colore è uno dei modi più efficaci per costruire un rapporto di fiducia a lungo termine con i tuoi clienti.
Hai riscontrato problemi di sbiadimento dei colori con le tue toppe o etichette? Condividi la tua esperienza o i tuoi consigli nei commenti: ci piacerebbe sapere come hai risolto il problema!